Abdominal shot molding refers to the procedure of injecting molten abdominal plastic into a mold at high stress and temperature levels. There are lots of ABS injection molding applications as it is an extensively used plastic and can be found in the automobile, customer item, and building sectors among others.
What is ABS Shot Molding?
ABS (Acrylonitrile Butadiene Styrene) injection molding is just one of the most preferred methods for making ABS plastic items. Abdominal muscle is a polycarbonate polymer that is durable and very easy to collaborate with. Shot molding is a process that entails injecting molten ABS right into a mold and mildew cavity. The ABS component cools down and is expelled. Injection molding is rapid and reliable, and it can be made use of to develop a variety of abdominal items. Very couple of making innovations can achieve the very same scale at the inexpensive provided by shot molding.
Abdominal muscle is widely utilized in shot molding as a result of its preferable buildings. These include high toughness, low melting temperature, recyclability, and good resistance to chemicals and warmth. It is likewise relatively easy to procedure and can be formed into a variety of sizes and shapes. Consequently, ABS is an ideal choice for applications in which strength and resilience are needed, such as: auto parts, family home appliances, tools, and clinical tools. On the whole, abdominal muscle is a flexible and prominent choice for injection molding.
Applications of ABS Injection Molding
Abdominal is made use of in several markets. Some usual industries and their pertinent applications are listed below.
Consumer Products: abdominal muscle is commonly utilized in the consumer sector. Typical items consist of Lego Ⓡ blocks and computer keyboard secrets. Abdominal muscle produces a smooth, glossy surface area that is unsusceptible dust impregnation. ABS will certainly react well to the inclusion of pigments and can be easily painted or perhaps electroplated if preferred.
Construction Market: abdominal muscle is utilized for real estates on many power tools because of its toughness. Power outlet installations are also often made from ABS.
Automotive market: ABS is usually made use of for components such as: dashboards, safety belt parts, door trim, and bumpers as a result of its reduced weight, durability, and stamina.
The ABS Shot Molding Refine
The abdominal muscle shot molding procedure is the same as the process involved with shot molding in a lot of various other thermoplastics. The ABS injection molding process starts with pellets of ABS material being fed right into a receptacle. The pellets are after that thawed and injected right into a mold under high pressure. When the molten abdominal muscle has actually cooled down and solidified, the part is expelled from the mold and the procedure is repeated. The abdominal muscle shot molding procedure is fairly basic and efficient, making it optimal for high-volume manufacturing runs. ABS likewise has great dimensional stability and can be conveniently machined or drilled after molding.
ABS Shot Molding Strategies
Listed below are some essential methods used for injection molding abdominal muscle parts with various qualities:
Thin-Walled Parts: ABS has a reasonably high thickness, and as such injection pressures need to be enhanced for thin-walled components. Past its plasticizing temperature, the viscosity of ABS will raise with increased temperature. Therefore, only pressure can be increased for thin-walled components. Molds must be especially designed to deal with these raised stress.
Large Hollow Components: Injection molding huge, slim, or hollow components is testing. It might be beneficial to take advantage of water-assisted or gas-assisted injection molding which enables the manufacture of huge, thin-walled, or hollow components. This technique utilizes high-pressure water or gas to push the molten plastic against the sides of the mold to create consistent density and smooth inner quantities.
Thick-Walled Parts: Manufacturing thick-walled get rid of standard shot molding strategies can generate sink marks on the part. One technique of getting around this is to make use of compression shot molding, which basically deposits a particular quantity of molten plastic right into a mold and mildew to generate the final part. This strategy also lowers inner stresses normal with shot molding. Conversely, sink marks can be taken care of with thinner (or more uniform) mold and mildew wall surfaces or raised thermal transfer capacity in the mold.
Multi Product: If multi-material components are required, then methods such as insert molding or overmolding can be used. Abdominal muscle is usually made use of for industrial tooling like cordless drills, which have their handles overmolded onto the abdominal to enhance device hold.
Advantages of ABS Injection Molding
The advantages of abdominal muscle injection molding are:
1. High Efficiency – Effectiveness
Shot molding is an extremely efficient and productive manufacturing innovation and is the recommended technique of manufacturing abdominal muscle parts. The procedure produces restricted waste and can generate large volumes of parts with limited human communication.
2. Layout of Complicated Components
Shot molding can generate multi-featured, complicated parts that can consist of steel inserts or overmolded soft-grip handholds. The intricacy of the parts is just restricted by a set of reputable style for production (DFM) standards created particularly for injection molding.
3. Increased Stamina
Abdominal is a solid, lightweight polycarbonate that is extensively made use of in a variety of markets due to these buildings. As such, injection molding in ABS is perfect for applications that require increased toughness and overall mechanical strength.
4. Versatility of Shade and Product
Abdominal is conveniently colored with a wide variety of shades; this is evident with Lego Ⓡ blocks which are made from abdominal muscle. It has to be noted, nonetheless, that ABS has inadequate weathering resistance and can be deteriorated by UV light and long term outside direct exposure. The good news is, ABS can be repainted and also electroplated with steel to improve its environmental resistance.
5. Lowered Waste
Shot molding is inherently low-wastage production modern technology as a result of the large manufacturing volumes that injection molding was created for. When numerous components are made each year, any kind of quantity of wastefulness adds up to a considerable price over time. The only waste is the material in the sprue, joggers, and the flashing in between mold halves.
6. Affordable of Labor
Due to the highly automated nature of shot molding, extremely limited human intervention is needed. Lowered human intervention results in minimized labor prices. This reduced labor expense eventually leads to an affordable per part.
Negative Aspects of ABS Injection Molding
The drawbacks of ABS injection molding are listed here:
1. High Tooling Costs and Extended Lead Times for Setup
Shot molding calls for the style and manufacture of molds whose cost and production time boost with component intricacy. As such, the initial financial investment in shot molding is high, and the price must be considered versus the expected manufacturing quantities. Lower manufacturing quantities may not be economically feasible.
2. Partial Design Limitations
Shot built component designs are limited by a collection of rules that were painstakingly developed to enhance shot built part quality and consistency. These rules specify wall density limitations, the place of enhancing features like ribs, and the ideal opening area and dimension. Therefore, styles should be made to adhere to these policies to guarantee ideal outcomes. In some cases, these guidelines can ensure styles impossible.
3. Pricey Small-Run Components Are an Opportunity
Due to the high preliminary financial investment price when injection molding, there is a minimum part quantity called for to break even on the prices expended on the layout and manufacture of the mold. This break-even point is also dependent on the designated sale price of the end product. If the sale price is high– because of the component being made use of for a specialized application– it might be possible to have small-run manufacturing. Nonetheless, inexpensive components call for high quantities in the 10s of thousands to be affordable.
Some Typical Troubles in ABS Shot Molding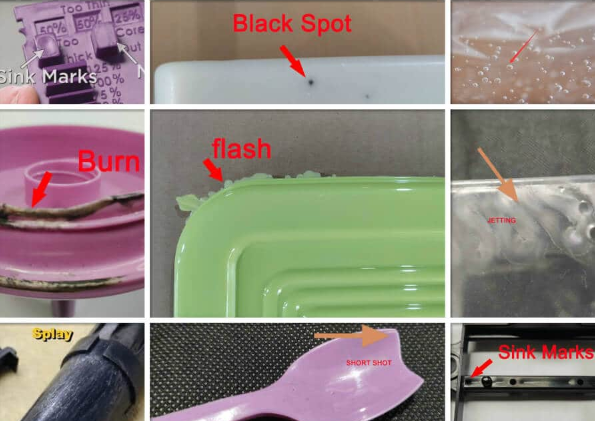
- Thickness: Unlike many various other amorphous plastics, the viscosity of ABS boosts when heated past its plasticizing temperature. This increase in thickness means that the thaw temperature level of abdominal muscle need to be maintained or below this temperature level for ideal results as boosted viscosity will certainly make it harder to mold and mildew thin-walled elements.
- Thermal Degradation: Aside from an undesirable rise in thickness with boosted temperature, ABS often tends to chemically weaken if kept at temperature levels much above its plasticizing temperature level.
- Bending: Bending takes place when abdominal plastic cools down erratically, leading to distortion. Contorting can be prevented by utilizing a mold and mildew with uniformly spaced air conditioning networks. Expeling parts from the mold and mildew before they have had a possibility to cool down completely can likewise result in warping.
- Sink Marks: Sink marks can take place when the abdominal muscle plastic shrinks unevenly throughout cooling, creating sunken locations on the surface of the component. Other possible causes can be inadequate injection pressure or extreme temperature level. Sink marks can be stopped by utilizing a mold with high gateway pressure, creating a part with consistent outer walls, and restricting inner strengthening ribs to around 50% of the density of the external walls.
Product Made Use Of for Injection Molding
Injection molding can be made use of with nearly any type of polycarbonate. Thermoplastics can be full of strengthening additives like glass or carbon fiber fillers. Metals can additionally be infused if integrated with a plastic filler material to enable the steel powder to stream through the mold. Nonetheless, extra sintering is required for steel injection molding.
Post time: Aug-29-2024