In order to determine whether 3D printing is better than injection molding, it’s worth comparing them against several factors: cost, volume of production, material options, speed, and complexity. Every technology has its weaknesses and strengths; therefore, which one to use depends solely on the requirements of the project.
Here is a comparison of 3D printing and injection molding to determine which one is better for the given situation:
1.Volume of Production
Injection Molding: High Volume Use
Injection molding is very suitable for large-scale production. Once the mold is made, it will produce thousands of millions of the same parts at an extremely fast speed. It’s highly efficient for large runs because parts can be produced with a very low cost per unit at a very rapid speed.
Suitable for: Large-scale production, parts where consistent quality is vital, and economy of scale for large quantities.
3D Printing: Best for Low to Medium Volumes
3D printing is suited for products requiring low to a medium run. Though the mold cost for setting up a 3D printer goes lower since a mold is not required, the cost for each piece remains reasonably higher for heavy volumes. Again, mass productions are not well suited, rather slower compared to an injection mold production and not possible to be economized by large batches.
Suitable for: Prototyping, small production runs, custom or highly specialized parts.
2.Costs
Injection Molding: High Initial Investment, Low per-unit cost
The initial setup is expensive to set up, as making custom molds, tooling, and machines is costly; once the molds have been created, however, the cost per part drastically goes down the more one produces.
Best for: High-volume production projects where the initial investment is recouped over time by reducing the cost of each part.
3D Printing: Lower Initial Investment, Higher Per-Unit Cost
The initial cost of 3D printing is relatively low since no molds or specialized tools are needed. However, the per-unit cost can be higher than injection molding, especially for large parts or higher volumes. Material costs, print time, and post-processing can add up quickly.
Ideal for: Prototyping, low-volume production, custom or one-off parts.
3.Flexibility in Design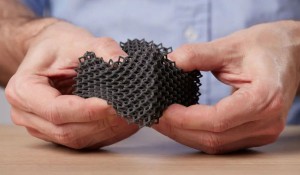
Injection Molding: Not so Versatile but Very Accurate
Once the mold is made, it is costly and time-consuming to change a design. Designers must consider the limitations of the mold in terms of undercuts and draft angles. However, injection molding can produce parts that have precise tolerances and smooth finishes.
Suitable for: Parts with stable designs and high precision.
3D Printing: Flexible Enough And Without The Requiring Molding Constraint
With 3D printing, you can create very complex and detailed designs that are not possible or economically feasible to do with injection molding. There is no limitation on the design like undercuts or draft angles, and you can make changes in a very short time without new tooling.
Best for: Complex geometries, prototypes, and parts that often undergo changes in the design.
4.Material Options
Injection Molding: Very Versatile Material Options
Injection molding supports a wide range of polymer, elastomers, polymer composites, and high-strength thermosets. This process is used for the production of strong functional parts with better mechanical properties.
Suitable for: Functional, durable parts of various plastics and composite materials.
3D Printing: Limited Materials, But on the Rise
Many materials, including plastics, metals, and even ceramics, are available for 3D printing. However, the number of material options is not as wide as those in injection molding. The mechanical properties of parts made through 3D printing can be different, and parts often exhibit less strength and durability than injection-molded parts, although this gap is decreasing with new developments.
Suitable for: Cheap prototypes; custom components; material-specific resin such as photopolymer resins and specific thermoplastics and metals.
5.Speed
Injection Molding: Quick for Mass Production
After it is ready, injection molding is relatively very fast. In fact, the cycle may only take a few seconds to several minutes for each to enable the quick production of hundreds and thousands of parts. However, it takes a longer time to set up and design the initial mold.
Ideal for: High-volume production with standard designs.
3D Printing: Much Slower, Especially for Bigger Items
Injection molding is significantly faster than 3D printing, particularly for larger or more complex parts. Printing each layer individually, it may take hours or even days for the larger or more detailed parts.
Suitable for: Prototyping, small parts, or complex shapes that do not require high-volume production.
6.Quality and Finish
Injection Molding: Good Finish, Quality
Parts produced by injection molding have a smooth finish and excellent dimensional accuracy. The process is very controlled, resulting in consistent high-quality parts, but some finishes may require post-processing or removal of excess material.
Suitable for: Functional parts with tight tolerances and good surface finishes.
Lower Quality and Finish with 3D Printing
The quality of 3D printed parts heavily depends on the printer and material used. All 3D printed parts exhibit visible layer lines and are in general post-processing required-sanding and smoothing-to provide a good surface finish. Resolution and precision of 3D printing are improving but might not be equivalent to injection molding for functional, high-precision parts.
Suitable for: Prototyping, parts that do not require a perfect finish, and designs that will be further refined.
7.Sustainability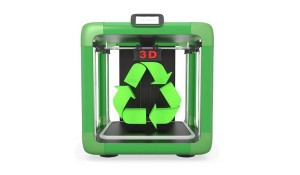
Injection Molding: Not as Sustainable
Injection molding produces much more material waste in the form of sprues and runners (unused plastic). Also, molding machines consume a significant amount of energy. However, efficient designs can minimize such waste. Still, many manufacturers now use recycled material in the injection molding process.
Ideal for: High volumes of plastic production, though sustainability efforts can be enhanced with better material sourcing and recycling.
3D Printing: Less Environmentally Degraded in Certain Cases
This also means that 3D printing can be much more sustainable, because it only uses the amount of material necessary to create the part, thereby eliminating waste. In fact, some 3D printers even recycle failed prints into new material. But not all 3D printing materials are equal; some plastics are less sustainable than others.
Suitable for: Low-volume, on-demand production Waste reduction.
Which Is Better for Your Needs?
Use Injection Molding if:
- You are running a high-volume production run.
- You need the strongest, longest-lasting, best quality, and consistency in parts.
- You have the capital for the upfront investment and can amortize mold costs over a large number of units.
- The design is stable and does not change much.
Use 3D Printing if:
- You require prototypes, low-volume parts, or highly customized designs.
- You need flexibility in design and rapid iteration.
- You require a cost-effective solution for producing one-off or specialized parts.
- Sustainability and savings in materials are a key issue.
In conclusion, 3D printing and injection molding both have their strengths. Injection molding boasts the advantage of producing in high quantity, whereas 3D printing is said to be flexible, prototyping, and low volume or highly customized production. It will boil down to what exactly the stakes are of your project—differing needs in terms of production, budget, timeline, and complexity of the design.
Post time: Feb-07-2025