Fracture strength is a fundamental property that plays a pivotal role in material science and engineering, helping to determine how a material will behave under stress, particularly when it undergoes failure. It provides insight into the maximum stress a material can withstand before it fractures, offering engineers and material scientists the data needed to select appropriate materials for different applications. In this comprehensive article, we will explore what fracture strength is, its significance, various modes of fracture, and how it can be tested in a manufacturing environment. Additionally, we will dive into challenges associated with fracture strength testing and the importance of understanding the stress-strain curve.
What is Fracture Strength?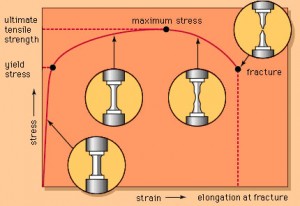
Fracture strength refers to the maximum amount of stress or force a material can endure before experiencing catastrophic failure, characterized by fracture. This failure occurs when the material’s internal structure is no longer able to handle the applied load, resulting in crack propagation that ultimately leads to a complete fracture. Typically expressed in units of pressure, such as pascals (Pa) or pounds per square inch (psi), fracture strength is an essential property that helps engineers predict how materials will perform under real-world conditions, especially in structural applications where failure could be catastrophic.
The fracture strength of a material depends on several factors, including its crystal lattice composition, alloy or composite structure, and the manufacturing processes involved. Materials exhibit varying levels of fracture strength, largely due to their atomic arrangement and the type of bonding between atoms.
Types of Materials Based on Fracture Strength:
- Brittle Materials: Concrete, ceramics, and gray cast iron are often strong under compression but exhibit low fracture strength. These materials can handle compressive forces well but fail easily under tensile or bending stresses.
- Ductile Materials: Mild steel, aluminum, and many polymers generally have lower compressive strength but higher fracture strength. These materials can deform plastically before failing, allowing them to absorb energy and withstand greater stresses without cracking.
Fracture strength can be altered significantly by external factors such as temperature, the rate at which loading occurs, the presence of defects or flaws in the material, and the nature of the applied stress (whether tensile, compressive, shear, etc.).
Modes of Fracture in Materials
Understanding the various modes of fracture helps in determining how a material will respond under different stress scenarios. The most common modes of fracture include tensile, compressive, and bending fractures. Each mode involves different stress distributions and failure mechanisms.
1. Tensile Fracture:
Tensile fracture occurs when a material is subjected to an external force that pulls it apart along a single axis. This type of fracture typically happens in materials under pure tension, and it is characterized by the separation or rupture of the material along a plane perpendicular to the applied tensile load.
- Initial Deformation: The material initially undergoes elastic deformation, where the material elongates in the direction of the applied load. The deformation is recoverable, meaning the material returns to its original shape once the force is removed.
- Necking: As the load increases, a localized region begins to deform more significantly. This phase, known as necking, causes a reduction in the cross-sectional area at the point of maximum stress. The material stretches, and its crystal boundaries slip.
- Ultimate Tensile Strength (UTS): The ultimate tensile strength refers to the maximum amount of stress the material can endure before the necked region becomes critical, causing the fracture to propagate rapidly across the entire cross-section.
2. Compressive Fracture:
Compressive fracture occurs when a material is subjected to forces that push it together along the load axis. This type of fracture results in bulging, crushing, and fragmentation of the material. Compressive fractures typically result in multiple fractures as the material struggles to resist the applied compressive stress.
- Elastic Deformation: In the initial phase, the material undergoes elastic deformation, which can recover once the load is removed. However, as the load increases, the material enters the plastic deformation phase.
- Plastic Deformation and Bulging: In ductile materials, compressive loads cause plastic deformation, which manifests as bulging perpendicular to the applied load. Brittle materials, in contrast, typically fracture once the elastic limit is exceeded, as they lack the ability to undergo significant plastic deformation.
- Ultimate Strength: When the material reaches its ultimate compressive strength, multiple cracks can develop, leading to fragmentation or collapse of the material under the applied load.
3. Bending Fracture:
Bending fracture occurs when a material is subjected to both tensile and compressive stresses, due to an external bending force. A typical bending fracture originates on the tensile side, where the material experiences elongation, and propagates through the thickness of the material.
- Tensile and Compressive Stresses: The outer fibers of the material (on the loaded side) experience tensile stresses, while the inner fibers (opposite the applied load) experience compressive stresses. These stresses induce a failure on the tensile side, where cracking or deformation is more likely.
- Crack Propagation: As the applied bending force increases, cracks initiate on the tensile side and may propagate completely through the material thickness, leading to failure.
Tests to Determine Fracture Strength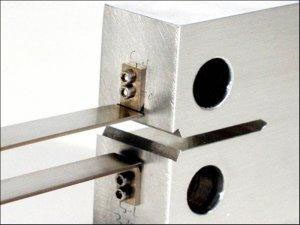
There are several standardized tests used to determine the fracture strength of materials. These tests are essential for understanding how a material will perform under various loading conditions. Common fracture strength tests include tensile, compression, and impact tests.
1. Tensile Test:
In a tensile test, a standardized sample with a necked (dog bone) shape is subjected to axial loading in pure tension. This test helps evaluate how the material responds to tension, providing data on its elastic and plastic phases, ultimate tensile strength (UTS), and elongation at break.
- Outcome: The UTS value represents the stress at which the material will fracture. The tensile test also provides information about ductility and the potential for plastic deformation.
2. Compression Test:
A compression test involves loading a standardized test block axially with pure compressive force. This test evaluates the material’s ability to resist compression and provides data on its compressive strength and compression modulus.
- Outcome: The test helps identify the point at which the material can no longer withstand the compressive force and begins to deform plastically or fail.
3. Impact Test:
Impact testing is conducted to evaluate a material’s ability to withstand sudden, dynamic loads. A sample, typically notched to promote crack initiation, is struck by a high-velocity impactor. The energy absorbed during impact or the extent of fracture is measured.
- Outcome: This test helps determine properties like impact strength and toughness, which are crucial for materials exposed to dynamic or shock loading conditions.
Benefits of Testing Fracture Strength in Manufacturing
Testing fracture strength provides essential insights that guide the selection of materials for specific applications. Some key benefits include:
- Identifying Weaknesses: Testing allows manufacturers to detect potential defects or weaknesses in materials that could lead to premature failure under certain conditions.
- Material Selection: Different materials exhibit varying fracture strengths, and understanding these behaviors helps engineers select materials that can withstand anticipated stresses in specific applications.
- Design Optimization: Fracture strength testing helps identify stress concentrations or weak points in a design, allowing engineers to optimize material selection and design geometry for better performance.
- Safety: Conducting fracture strength tests helps identify materials that could fail under specific loading conditions, mitigating risks in critical applications such as aerospace, automotive, and medical devices.
Challenges of Testing Fracture Strength in Manufacturing
Despite its significance, testing fracture strength in manufacturing presents several challenges:
- Material Variability: Even within the same production batch, material properties can vary, leading to discrepancies in fracture strength testing results. As production scales, commoditization of materials can introduce hidden variability.
- Sample Size and Geometry: The size and shape of the test sample significantly affect fracture strength results. Small test samples may not accurately represent the behavior of larger components, especially when complex geometries are involved.
- Loading Conditions: Fracture strength can vary depending on the loading condition, making it challenging to simulate real-world stress scenarios in laboratory tests.
- Environmental Factors: Factors such as temperature, humidity, and chemical exposure can affect a material’s fracture strength. Testing under controlled environmental conditions requires specialized equipment.
- Strain Rate Sensitivity: Some materials exhibit rate-dependent fracture properties, meaning the fracture strength can vary based on how quickly the load is applied, complicating test results.
The Stress-Strain Curve and Fracture Strength
The stress-strain curve graphically represents the relationship between applied stress and the resulting strain in a material. It provides valuable information on how a material deforms under load and helps engineers understand the material’s mechanical behavior, especially in terms of its fracture strength.
- Elastic Deformation: In the initial phase of loading, the material undergoes elastic deformation, where stress and strain are proportional. Upon removing the load, the material returns to its original shape.
- Plastic Deformation: As stress increases, the material enters the plastic deformation region, where the material experiences permanent changes in shape.
- Ultimate Strength and Fracture Point: The point at which the material can no longer withstand the applied load is known as the fracture point, often denoted on the stress-strain curve as the ultimate tensile strength (UTS).
Characteristics and Types of Fracture
The characteristics of fracture can provide valuable insight into the material’s behavior under stress. Key features include:
- Cleavage Planes: Smooth, flat planes along which the material breaks, often along crystal boundaries.
- Dimples: Round depressions on the fracture surface, indicative of ductile fracture and energy absorption.
- Shear Lips: Fracture surfaces exhibiting fibrous or powdery textures, characteristic of micro-void coalescence.
- Hackles: Chevron patterns on the fracture surface that indicate the direction of crack propagation.
Fracture Strength of Ceramics and Glass
Materials like ceramics and inorganic glass exhibit distinct fracture behaviors due to their atomic structures.
- Ceramics: Known for their high strength and stiffness, ceramics are also highly brittle. They have strong atomic bonds but limited ability to deform plastically, making them prone to sudden fracture when exposed to critical stress levels.
- Inorganic Glass: Unlike ceramics, inorganic glass (e.g., silica glass) has an amorphous structure, leading to a more uniform distribution of stress. While it has higher fracture strength than ceramics, it is also highly sensitive to surface defects that can dramatically reduce its strength.
Conclusion
Fracture strength is a critical material property that engineers and material scientists must consider when designing components or structures that will undergo significant stress. Understanding the fracture strength of materials and the factors that influence it can help optimize material selection, enhance product safety, and improve design efficiency. Whether through tensile, compressive, or impact testing, accurate evaluation of fracture strength is vital for ensuring the reliability and durability of products in industries ranging from aerospace to medical devices.
Post time: Jan-25-2025