実現可能なプラスチック部品を設計する方法
新しい製品について非常に良いアイデアがありましたが、図面を完成させた後、サプライヤーからこの部品は射出成形できないと言われました。新しいプラスチック部品を設計するときに注意すべき点を見てみましょう。
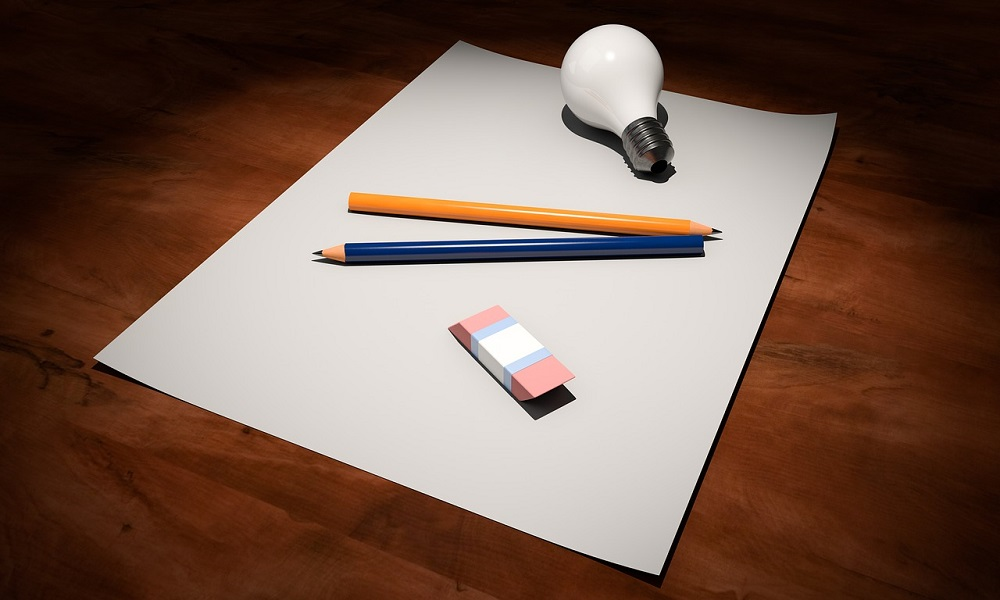
壁の厚さ –
たぶん全部プラスチック射出成形エンジニアは壁の厚さをできるだけ均一にすることを提案します。理解するのは簡単ですが、厚いセクターは薄いセクターよりも大きく収縮し、反りやヒケが発生します。
部品の強度と経済性を考慮し、十分な剛性がある場合には、肉厚を可能な限り薄くする必要があります。壁の厚さを薄くすると、射出成形部品の冷却が速くなり、部品の重量が軽減され、製品の効率が向上します。
独特の肉厚が必要な場合は、肉厚を滑らかに変化させ、ヒケや反りの問題を回避するために金型構造の最適化を試みてください。
コーナー –
角の太さが通常の太さよりも厚くなるのは明らかです。したがって、一般的には、外側のコーナーと内側のコーナーの両方に半径を使用して、鋭いコーナーを滑らかにすることをお勧めします。溶融プラスチックの流れは、湾曲したコーナーを通過するときに抵抗が少なくなります。
リブ –
リブはプラスチック部品を強化することができ、もう 1 つの用途は、長くて薄いプラスチック ハウジングのねじれの問題を回避することです。
厚さは壁の厚さと同じではなく、壁の厚さの約 0.5 倍をお勧めします。
リブベースには半径と 0.5 度の抜き勾配が必要です。
リブを近づけすぎず、肉厚の2.5倍程度の間隔をあけてください。
アンダーカット –
アンダーカットの数を減らすと、金型設計が複雑になり、故障のリスクも高まります。
投稿時間: 2021 年 8 月 23 日