Абдоминальное дробление относится к процедуре впрыскивания расплавленного абдоминального пластика в форму при высоком напряжении и температуре. Существует множествоЛитье под давлением АБСприменения, поскольку это широко используемый пластик, который можно найти в автомобильной промышленности, производстве потребительских товаров и строительстве, в том числе и в других отраслях.
Что такое литье под давлением АБС?
Литье под давлением ABS (акрилонитрил-бутадиен-стирол) является одним из наиболее предпочтительных методов изготовления изделий из ABS-пластика. Брюшная мышца представляет собой поликарбонатный полимер, который долговечен и с которым очень легко работать. Выдавливание представляет собой процесс, который подразумевает впрыскивание расплавленного ABS прямо в форму и полость плесени. Компонент ABS охлаждается и выталкивается. Литье под давлением является быстрым и надежным, и его можно использовать для разработки различных предметов брюшной полости. Очень немногие инновации в производстве могут достичь того же масштаба по доступной цене, предоставляемой выдавливанием под давлением.
Брюшная мышца широко используется в литье под давлением из-за ее предпочтительных свойств. К ним относятся высокая прочность, низкая температура плавления, пригодность к переработке и хорошая устойчивость к химикатам и теплу. Она также относительно проста в обработке и может быть сформирована в различные размеры и формы. Следовательно, ABS является идеальным выбором для применений, в которых требуются прочность и упругость, например: автозапчасти, бытовая техника, инструменты и клинические инструменты. В целом, брюшная мышца является гибким и выдающимся выбором для литья под давлением.
Применение литья под давлением АБС
Абдоминальный используется на нескольких рынках. Некоторые обычные отрасли и их соответствующие приложения перечислены ниже.
Потребительские товары: брюшная мышца обычно используется в потребительском секторе. Типичные предметы состоят из блоков Lego Ⓡ и секретов компьютерной клавиатуры. Брюшная мышца производит гладкую, глянцевую поверхность, которая невосприимчива к пропитке пылью. ABS, безусловно, хорошо реагирует на включение пигментов и может быть легко окрашен или, возможно, гальванизирован, если это желательно.
Строительный рынок: брюшная мышца используется для недвижимости на многих электроинструментах из-за ее прочности. Установки розеток также часто изготавливаются из ABS.
Автомобильный рынок: ABS обычно используется для таких компонентов, как приборные панели, детали ремней безопасности, обивка дверей и бамперы, благодаря своему малому весу, прочности и выносливости.
АБС-пластиковое литье под давлением
Процедура литья под давлением брюшной мышцы такая же, как и процесс, связанный с литьем под давлением во многих других термопластиках. Процесс литья под давлением ABS начинается с подачи гранул материала ABS в емкость. После этого гранулы размораживаются и впрыскиваются в форму под высоким давлением. Когда расплавленная брюшная мышца фактически остывает и затвердевает, деталь выталкивается из формы, и процедура повторяется. Процедура литья под давлением брюшной мышцы довольно проста и эффективна, что делает ее оптимальной для крупносерийного производства. ABS также имеет большую размерную стабильность и может легко обрабатываться или сверлиться после формования.
Стратегии дробеструйного формования АБС
Ниже перечислены некоторые основные методы, используемые для литья под давлением частей мышц живота с различным качеством:
Тонкостенные детали: ABS имеет достаточно большую толщину, и поэтому для тонкостенных компонентов необходимо увеличить давление впрыска. После температуры пластификации вязкость ABS будет расти с повышением температуры. Поэтому для тонкостенных компонентов можно увеличивать только давление. Формы должны быть специально спроектированы для работы с этими повышенными напряжениями.
Большие полые компоненты: Тестируется литье под давлением больших, тонких или полых компонентов. Может быть полезно использовать преимущества водяного или газового литьялитье под давлениемчто позволяет производить огромные, тонкостенные или полые компоненты. Эта технология использует воду или газ под высоким давлением для прижимания расплавленного пластика к стенкам формы для создания постоянной плотности и гладких внутренних объемов.
Толстостенные детали: Изготовление толстостенных деталей избавьтесь от стандартных стратегий литья под давлением может привести к образованию утяжин на детали. Один из методов решения этой проблемы заключается в использовании компрессионного литья под давлением, которое в основном помещает определенное количество расплавленного пластика прямо в форму и плесень для создания конечной детали. Эта стратегия также снижает внутренние напряжения, обычные для литья под давлением. И наоборот, утяжины можно устранить с помощью более тонкой (или более однородной) поверхности стенок формы и плесени или повышенной теплопередающей способности формы.
Multi Product: Если требуются компоненты из нескольких материалов, то можно использовать такие методы, как вставное формование или многослойное формование. Брюшная мышца обычно используется для промышленных инструментов, таких как беспроводные дрели, ручки которых впрессованы в брюшную полость для улучшения удерживания устройства.
Преимущества литья под давлением АБС
Преимущества инъекционного формования мышц живота:
1. Высокая эффективность – результативность
Формование дробью является чрезвычайно эффективной и производительной производственной инновацией и является рекомендуемой технологией изготовления частей брюшных мышц. Процедура дает ограниченные отходы и может генерировать большие объемы деталей с ограниченным человеческим общением.
2. Расположение сложных компонентов
Формование дробьюможет генерировать многофункциональные, сложные детали, которые могут состоять из стальных вставок или переформованных мягких захватов. Сложность деталей ограничивается только набором стандартов авторитетного стиля для производства (DFM), созданных специально для литья под давлением.
3. Увеличение выносливости
Abdominal — это прочный, легкий поликарбонат, который широко используется на различных рынках из-за этих зданий. Таким образом, литье под давлением в ABS идеально подходит для приложений, требующих повышенной жесткости и общей механической прочности.
4. Универсальность оттенка и продукта
Брюшная полость удобно окрашена в широкий спектр оттенков; это очевидно на примере кубиков Lego Ⓡ, которые сделаны из брюшных мышц. Тем не менее, следует отметить, что ABS имеет недостаточную устойчивость к атмосферным воздействиям и может быть испорчена ультрафиолетовым светом и длительным прямым воздействием. Хорошей новостью является то, что ABS можно перекрашивать, а также гальванизировать сталью для повышения его устойчивости к воздействию окружающей среды.
5. Сокращение отходов
Литье под давлением по своей сути является современной технологией производства с малыми отходами, что обусловлено большими объемами производства, для которых было создано литье под давлением. Когда ежегодно изготавливается множество компонентов, любое количество отходов со временем выливается в значительную цену. Единственными отходами являются материал в литнике, толкателях и заусенцах между половинками пресс-формы.
6. Доступность рабочей силы
Из-за высокой степени автоматизации процесса формования впрыском требуется крайне ограниченное вмешательство человека. Снижение вмешательства человека приводит к минимизации затрат на рабочую силу. Это снижение затрат на рабочую силу в конечном итоге приводит к доступной цене за деталь.
Отрицательные аспекты литья под давлением АБС
Недостатки литья АБС-пластика под давлением перечислены ниже:
1. Высокие затраты на оснастку и длительное время наладки
Для литья под давлением требуется стиль и изготовление форм, стоимость и время производства которых увеличиваются с увеличением сложности компонентов. Таким образом, первоначальные финансовые вложения в литье под давлением высоки, и цену следует рассматривать в сравнении с ожидаемыми объемами производства. Более низкие объемы производства могут быть экономически нецелесообразны.
2. Частичные ограничения конструкции
Конструкции компонентов, изготовленных методом дробеструйной обработки, ограничены набором правил, которые были тщательно разработаны для повышения качества и согласованности деталей, изготовленных методом дробеструйной обработки. Эти правила определяют ограничения плотности стенок, место улучшения таких элементов, как ребра, и идеальную площадь и размер отверстия. Поэтому стили должны соответствовать этим политикам, чтобы гарантировать идеальные результаты. В некоторых случаях эти рекомендации могут сделать стили невозможными.
3. Дорогие мелкосерийные компоненты — это возможность
Из-за высокой предварительной стоимости финансовых инвестиций при литье под давлением существует минимальное количество деталей, необходимое для безубыточности по ценам, затраченным на макет и изготовление формы. Эта точка безубыточности также зависит от назначенной цены продажи конечного продукта. Если цена продажи высока — из-за того, что компонент используется для специализированного применения — возможно, можно иметь мелкосерийное производство. Тем не менее, недорогие компоненты требуют больших объемов в десятки тысяч, чтобы быть доступными.
Некоторые типичные проблемы при литье под давлением АБС-пластика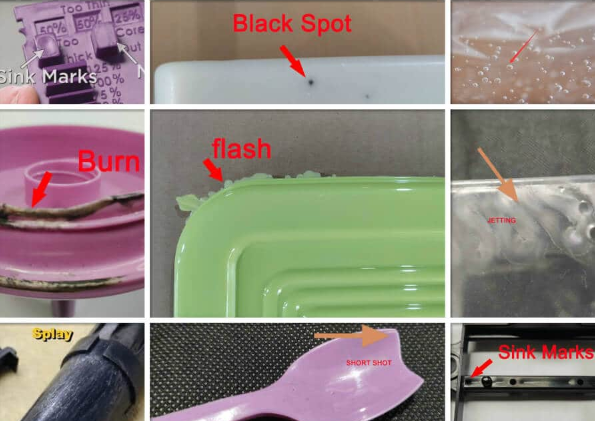
- Толщина: В отличие от многих других аморфных пластиков, вязкость ABS увеличивается при нагревании выше температуры пластификации. Это увеличение толщины означает, что уровень температуры оттаивания брюшных мышц должен поддерживаться или быть ниже этого уровня температуры для идеальных результатов, поскольку повышенная вязкость, безусловно, затруднит формование и гниение тонкостенных элементов.
- Термическая деградация: Помимо нежелательного увеличения толщины при повышении температуры, АБС часто имеет тенденцию к химическому ослаблению, если его хранить при температурах, значительно превышающих температуру его пластификации.
- Изгиб: Изгиб происходит, когда пластик брюшной полости охлаждается неравномерно, что приводит к деформации. Деформацию можно предотвратить, используя форму и плесень с равномерно расположенными сетями кондиционирования воздуха. Извлечение деталей из формы и плесень до того, как они полностью остынут, также может привести к деформации.
- Утяжины: Утяжины могут возникнуть, когда пластик брюшных мышц неравномерно сжимается во время охлаждения, создавая впадины на поверхности компонента. Другими возможными причинами могут быть недостаточное давление впрыска или экстремальный уровень температуры. Утяжины можно остановить, используя форму с высоким давлением шлюза, создавая деталь с постоянными внешними стенками и ограничивая внутренние ребра жесткости примерно 50% от плотности внешних стенок.
Продукт, используемый для литья под давлением
Литье под давлением можно использовать практически с любым типомполикарбонат. Термопластики могут быть полны упрочняющих добавок, таких как наполнители из стекла или углеродного волокна. Металлы могут быть дополнительно введены, если они интегрированы с пластиковым наполнителем, чтобы позволить стальному порошку течь через форму. Тем не менее, для литья стали под давлением требуется дополнительное спекание.
Время публикации: 29-авг-2024